For decades, surface engineering has played a crucial role in manufacturing plastic parts, refining how products feel, function and perform.
Meanwhile, laser engraving textures onto molds has long been a reliable tool for adding detail and precision. But in isolation, neither of these technologies is new. The real revolution is happening not with individual processes, but in how they are now being strategically combined to reshape the future of manufacturing.
What’s emerging is a three-part transformation: the fusion of advanced micro and nano-scale textures, the mastery of new part manufacturing techniques, and the integration of next-generation forming materials. This trifecta is unlocking unprecedented possibilities for product performance, aesthetics and efficiency, fundamentally altering how industries approach design and production and increase the value of the product offered to the end user.
The Evolution of Surface Engineering
The surface of a product is more than just its outermost layer—it’s the skin of the part. Like human skin, it does much more than serve as a boundary, it’s a vital organ with important functions. It protects, reacts to environmental conditions, enhances usability, and defines appearance. Whether it’s a smartphone case designed for grip and scratch resistance, an automotive panel engineered to reduce drag, or a medical device that repels bacteria, surface textures are integral to functionality.
Traditionally, manufacturers have relied on mechanical or chemical methods to create surface textures. These methods, while effective, often lacked the precision and repeatability needed to push the boundaries of design and performance. The rise of femtosecond and nanosecond laser engraving has changed the game, allowing for the direct creation of incredibly fine, repeatable, and highly controlled surface textures.
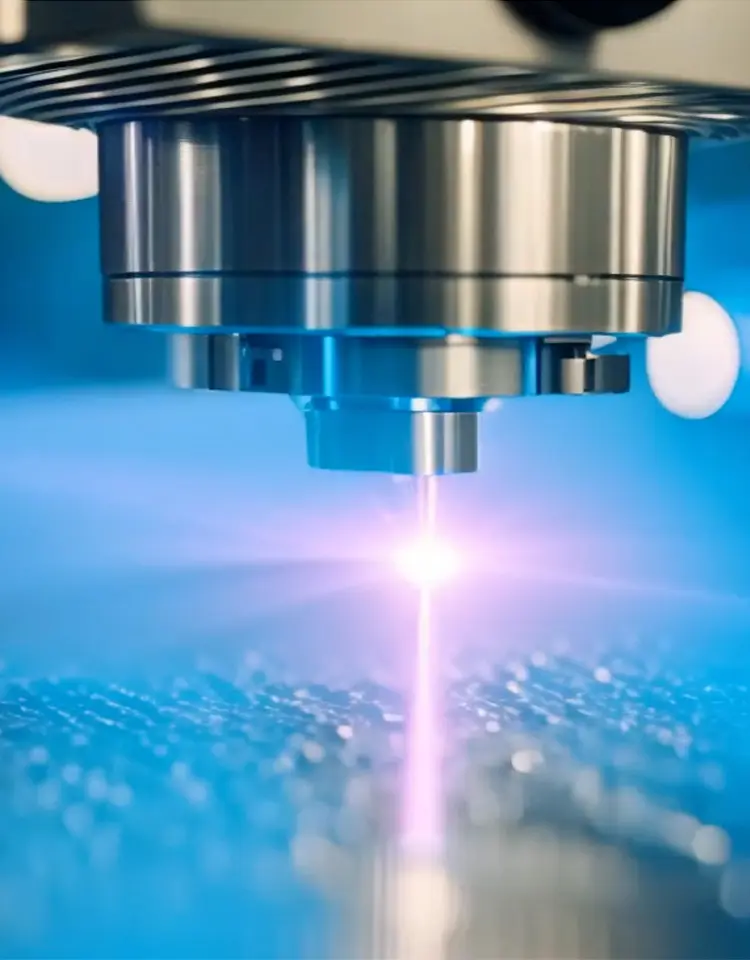
R&D Surface Innovation Three-Part Formula
Laser engraving alone isn’t the full story. It’s the convergence of three elements that is truly driving innovation:
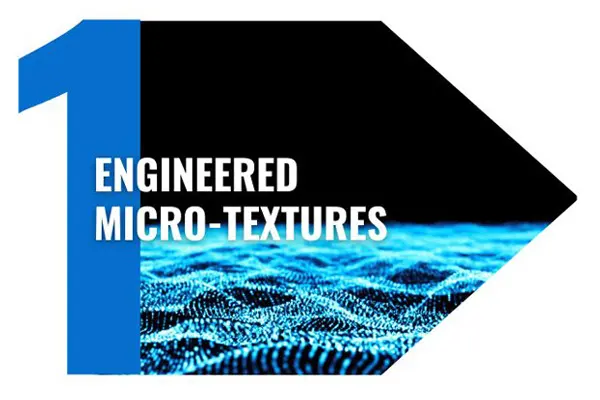
New Design-Engineered Micro and Nano Textures
Modern laser technology allows for the precise engraving of functional textures at the microscopic level. These textures can manipulate how surfaces interact with light, liquids and touch. From ultra-low friction surfaces to self-cleaning materials, the ability to design and control surface properties at this scale is a game-changer.
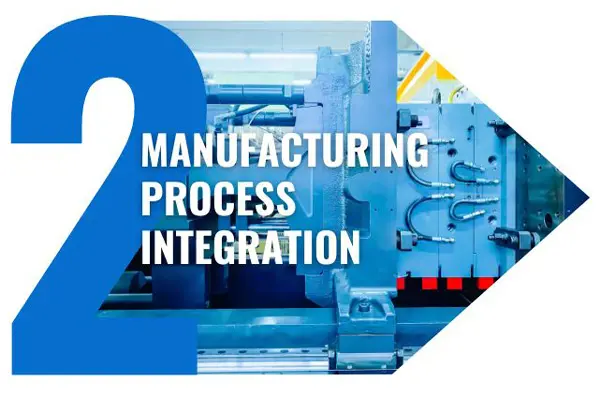
Advanced Manufacturing Process Integration
Texture alone doesn’t define success. The real challenge is integrating these new surfaces into existing or novel production methods. Expertise in molding, forming, and process control is essential to ensure that micro-engraved textures translate effectively from mold to final product without loss of detail or performance.
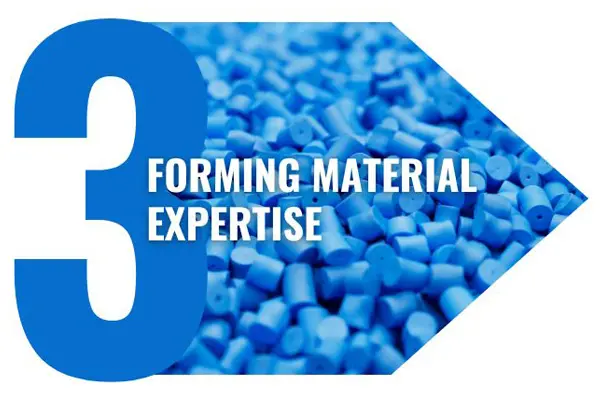
Innovative Forming Materials
The final piece of the puzzle is material selection. Today’s high-performance polymers, composites, and hybrid materials react differently to surface textures. By engineering materials to work in tandem with nano-engraved molds, manufacturers can unlock entirely new functional benefits—whether that means stronger, lighter, or more sustainable products.
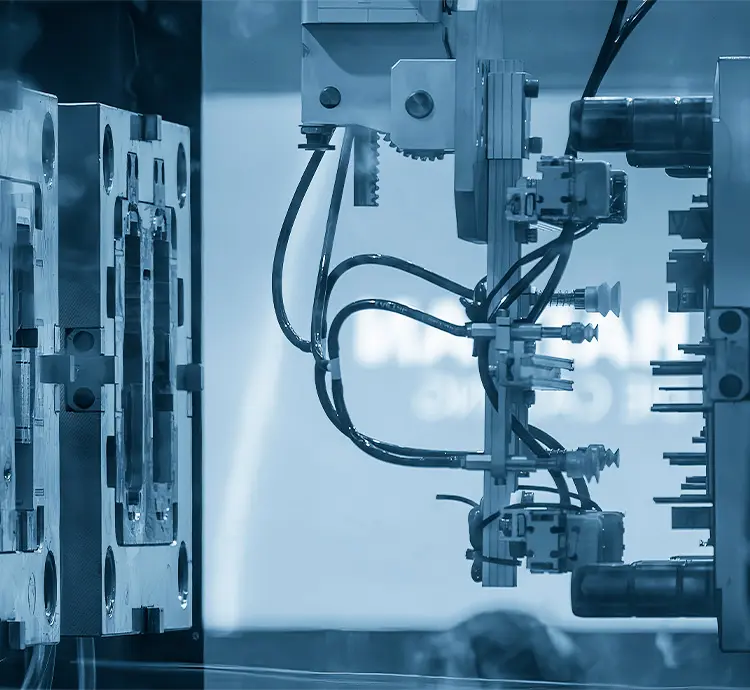
What This Means for Manufacturing
This new holistic approach is transforming industries. In consumer electronics, next-gen surface treatments are making devices more durable and comfortable to hold. In medical technology, antimicrobial surface textures are improving hygiene and safety.
The impact of this three-part approach isn’t just about better products—it’s about redefining how we manufacture. As companies embrace this new way of thinking, the role of surface engineering is shifting from an afterthought to a critical element in product innovation.
A New Era of Design and Manufacturing
We are entering an era where surface design is no longer limited by traditional constraints. By harnessing the power of laser-engraved textures, advanced manufacturing techniques, and material science, manufacturers are unlocking a new dimension of possibility. The surface of a product is no longer just an aesthetic choice—it’s an active, engineered layer with the power to enhance performance, efficiency, and user experience in ways we’re only beginning to explore.
The future of manufacturing isn’t just about what we make—it’s about how we shape the surfaces of the products that shape our world.
Unlock Cutting-edge Expertise in Texturing, Materials & Manufacturing
At Standex Engraving Mold-Tech, we don’t just offer surface texturing—we redefine what’s possible. As the global leader in engraving and texturing solutions, we invite you to collaborate with our Research & Development team to push boundaries and create groundbreaking results.
With our specialized R&D team at your side, you gain exclusive access to:
- Micro Surface Design and Engraving – Precision-engraved textures designed with a purpose, proven by research and developed for advanced performance.
- Material Mastery – Optimize forming materials with precision quality checks that save time and cost.
- Manufacturing Excellence – Enhance efficiency and repeatability with expert-driven process optimization.
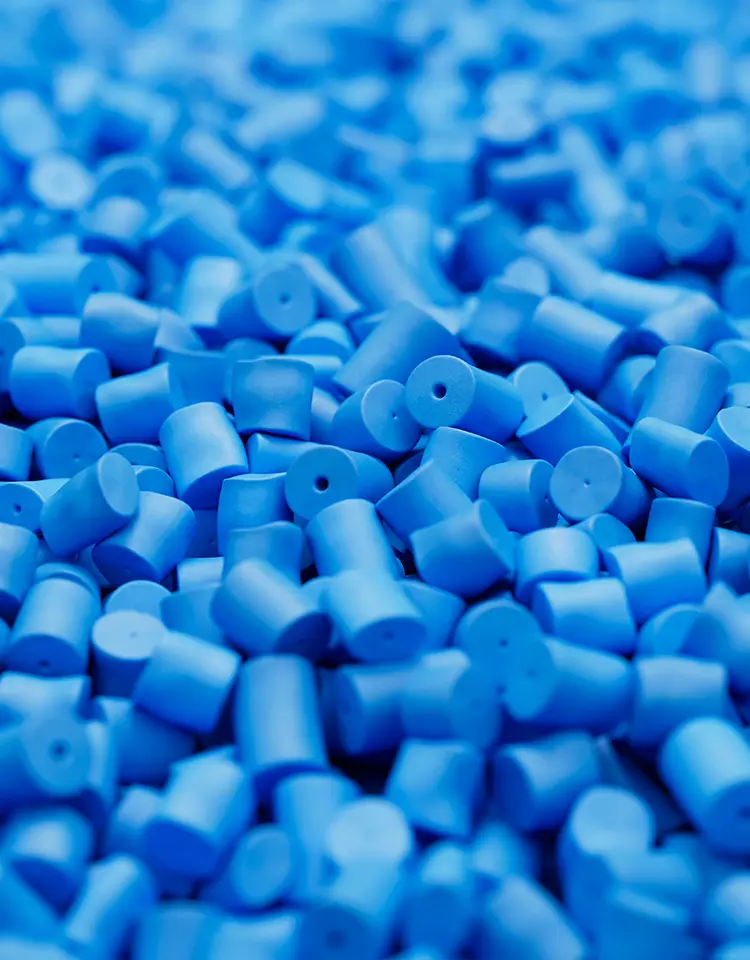
Global Innovation, Local Expertise
With operations worldwide, we bring cutting-edge technology and deep expertise to every region, ensuring seamless collaboration wherever you are.
Let’s turn your surfaces into high-performance assets that drive impact and customer loyalty. Schedule a call today and start shaping the future.